Introduction
Silicone micro molding is the latest trend in LSR manufacturing industry, in order to satisfy various small size silicone production requirement. As miniaturization development in many high-tech industries, components size is becoming more and more small. Therefore, this encourages silicone molding manufacturers must produce silicone parts with incredible accuracy and precision.
Liquid silicone rubber (LSR) injection molding has excellent tolerance and design flexibility. So LSR micro molding is the perfect solution for complex, tiny and critical silicone components. Otherwise, we also need to follow the guideline of LSR micro molding, analyze its benefits and challenges, and achieve the highest performance of final parts.
What is Silicone Micro Molding?
Silicone micro molding is a specialized silicone molding process, it is only suitable technology for high accuracy and high-precision silicone parts. These silicone parts are in minuscule size, the normal diameters are less than 4 mm or the weight is less than 1 gram.
Same as common LSR injection molding process, this process starts with tooling. The precise molds with small cavities contain the required sharp of design components. Then, liquid injection molding (LIM) technology will inject LSR into heated mold cavities. Finally, liquid silicone will solidify and cure in molds, then form required shape parts.
In LSR injection process, we apply two different devices to transfer liquid silicone materials. Firstly, we apply a runner system to direct LSR into the cavity. Alternatively, we also can use direct gating techniques, this will inject LSR material directly to cavities through gates.
LSR Micro Molding
In silicone micro molding, there are tremendous accuracy and precision requirement in both mold manufacturing and silicone part production. Due to small dimensions of part size, any tiny or minor errors will give rise to significant effects on final quality. In addition, LSR micro molding requires extra precision in component A & B mixing, color adding, and dose controlling. In order to guarantee LSR production stability and repeatability.
Therefore, all devices in LSR micro molding must have capability of utmost precise control in mixing, dosing and closing process. These devices including: feeding system, molds, molding system. Furthermore, we also need to control demolding process by cavity separation for containment and trace-ability. At last, magnifying devices are applied for handing and inspection of tiny tacky LSR parts. All these devices equipment require a high skill and expertise team, Miwo engineering team is able to innovate in the critical dimension of micrometer.
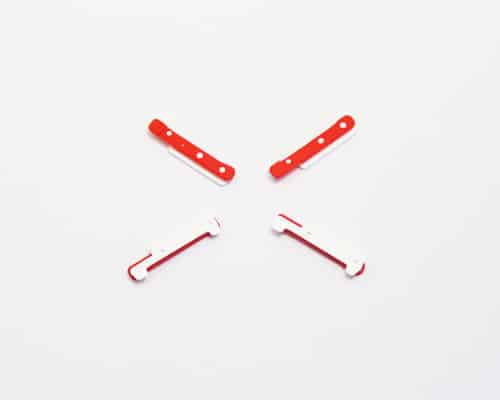
Why LSR is Beneficial for Micro Molding?
LSR has natural low viscosity, it is easy to fill small cavities. This is the primary reason that LSR is beneficial in micro injection molding. In addition, LSR has flexible characteristics, it is ideal for sealing applications with high elasticity and compressibility demand.
Micro Shot Weight
Miniaturization results to many challenges in LSR injection molding process. The most critical challenge is shot weight, it is the weight of one shot materials in injection molding process. We must determine the optimal shot weight by parameter of LSR part weight, runner weight and cavities number. Micro shot weight is critical for micro LSR molding, especially for tiny LSR parts with specific requirements.
Cool Barrel Temperature
As micro molding produces very small parts, the shot weight is very low. This gives rise to long time duration of polymer material staying in barrels. Furthermore, this long time expose will cause degradation of polymers. However, because of cool temperature in LSR barrels, LSR materials do not degrade or cure.
LSR Micro Molding Products
- Medical LSR parts: LSR micro molding is a cost-effective technology for medical LSR parts, especially for small parts with high performance. Such as: surgical devices, drug delivery devices, hearing aids.
- Electronic LSR parts: LSR micro molding is suitable for insulators, air tightness parts, water tightness parts.
- Automotive LSR parts: LSR micro molding can produce small automotive parts with weight constraints. Such as: micro seals, small switches, micro connectors.
Mold Construction Challenges
Precise control in LSR micro molding give rise to various challenges for product engineers. There are several engineering challenges in mold construction for LSR micro molding.
Accuracy
Micro injection molds requires accurate micro details and precise dimension to avoid any mismatch once mold is closing. Therefore, its electrical discharge machining (EDM) manufacturing process is more precise than normal tooling.
Assembly & Disassembly
Micro injection molds have tiny features for accurate alignment, these precise components are fragile and easy-breakable. Therefore, we need deliberate and delicate assembly & disassembly methods to avoid any defect in process.
Design
Mold design is the major challenge of mold construction, it must contain critical feature details with tiny dimension. In order to guarantee consistent alignment of mold halves in injection molding and precise demolding in removal. Furthermore, the mold design also ensures consistent quality and longevity for high-capacity production. A typical micro mold is able to finish millions of parts in its lifespan.
Pressure Balance
It is critical to balance cavity in the cold deck, in order to ensure consistent filling in micro molding process. For example, well-balanced cold deck and excellent valve gate technology can provide synchronous closing of needles, then avoid defect filling or short shot.
Temperature Management
Cavity temperature impact LSR material curing and parts formation. Nozzle cooling technology can cool the tip or beginning of the cavity, then assist transition from cooling in filling to heating in vulcanization. In addition, this technology is beneficial for proper filling.
Gating
We normally apply direct gating for components with adequate landing space. While sometimes, we must develop alternative in-direct gating solution for specific geometries without direct gates permit. Such as: film, edge, or tunnel gate.
Optimize Overflow
Overflows is normally applied to reduce air trapped risk, in order to ensure molds proper function. We also can use runners to facilitate parts operation in multistep operations, for example: laser marking, pad printing, packing, and assembly.
LSR Molding Challenges
Precise dimension in LSR micro molding present particular challenges for engineers in injection molding process..
Inspection Fluctuations
It is critical to monitor inputs and output for inspection fluctuations. Minimizing fluctuations is necessary in reason of slight deviations will impact final micro parts features.
LSR Materials Feeding
LSR material is consisted of component A & B normally, one component contains cross linker, and another contains platinum catalyst. We should manage the precise feeding of component A&B, exact 1:1 ratio is essential for proper blending and curing reaction.
Controlling Additive
In LSR micro molding, it is vital to control the third-stream flow of color pigment or other additives, even in low dosing rates. Only precise controlling can achieve excellent performance of final micro parts.
Demolding and Removing
As LSR parts are tacky, the removal process is a huge challenge in micro molding. Normally, we apply additional tools to fix this problem. However, for high cavitation molds, manual removal is another efficient method.
Part Inspection
As micro molded parts are in tiny size, orientation and inspection of delicate features are very difficult. We apply image measuring instrument for parts dimension inspection.
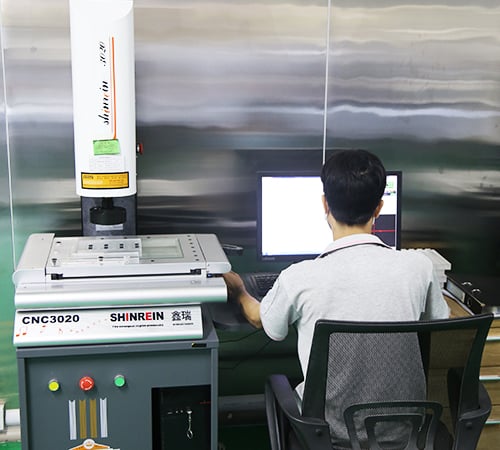
Why Choose Miwo for Micro Molding
Silicone micro molding is a complex technology, it consists of precision molds, fin-turned cells and advanced experience. Miwo is one of the best LSR molding manufacturer in China, we are popular for our precision and accuracy LSR parts manufacturing. Our engineering team has extensive experience in a wide of industries, we are able to satisfy any requirement of intricate geometries and mass production. No matter micro molding in LSR injection molding, LSR 2-shot molding, or LSR over-molding.