Silicone Compression Molding
- 12 Compression Molding Machines
- Foxconn & Target Products
- ODM Silicone Ties
Introduction
Miwo produces silicone compression molding components to service specialty applications for customers in worldwide. As our core business focus on silicone rubber technology. Our strength of silicone compression molding including silicone rubber compression molding, fluoro-silicone compression molding, and electrical conductive compounds molding. We apply silicone compression molding technology to produce micro-molded medical parts with complex details and tight tolerances.
Silicone compression molding is a labor-intensive production activity. It is applied to mold silicone rubber components from the starting of rubber manufacturing industry. This is one of the oldest methods still applied to rubber parts production. Miwo, as a silicone molding company, has utilized compression molding to custom silicone rubber parts. We provide an effective and efficient way to manufacture silicone rubber parts, no matter low-volume or high-volume production
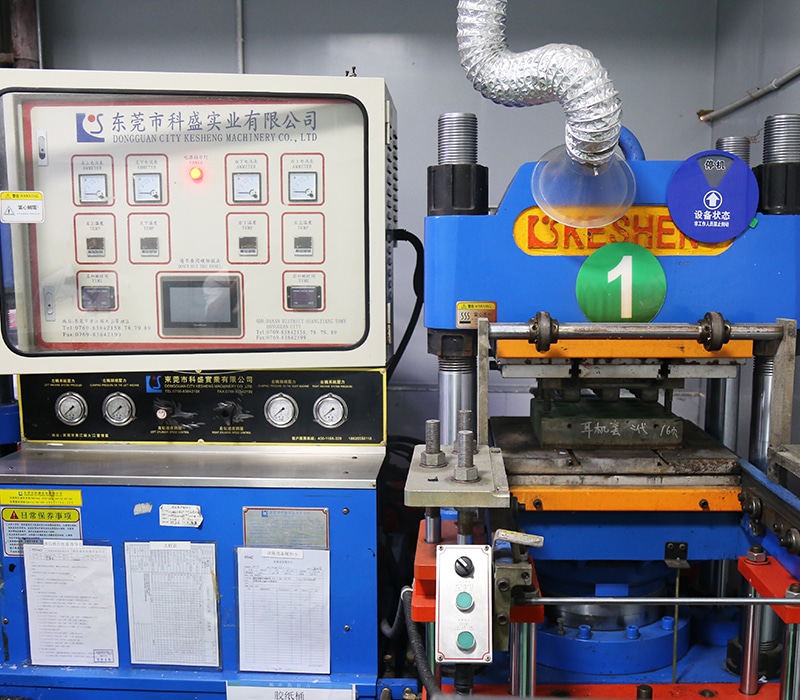
Silicone Compression Molding Process
Silicone compression molding process is more simple once compared to LSR injection molding, silicone transfer molding or extrusion molding.
- Firstly, we will manufacture a compression mold with CNC machining and polishing. In simple silicone parts design, there will be a two plates mold includes a cavity side and a core side. Then, mold plates will be assembled and inserted into a compression molding machine.
- After that, silicone materials like HCR (High Consistency Rubber) or LSR (Liquid Silicone Rubber) will be loaded into mold plates, compression machines will set heat and pressure with according time, allow silicone materials to spread throughout mold cavities and solidify.
- Finally, release pressure from compression press, then separate mold plates and remove silicone parts. This is a normal compression molding cycle for simple silicone parts.
Miwo has different size of compression molding presses. This guarantee our capability from small to large size rubber parts, single cavity molds to multi-cavity molds. We can configure our molding equipment to satisfy different production demands.
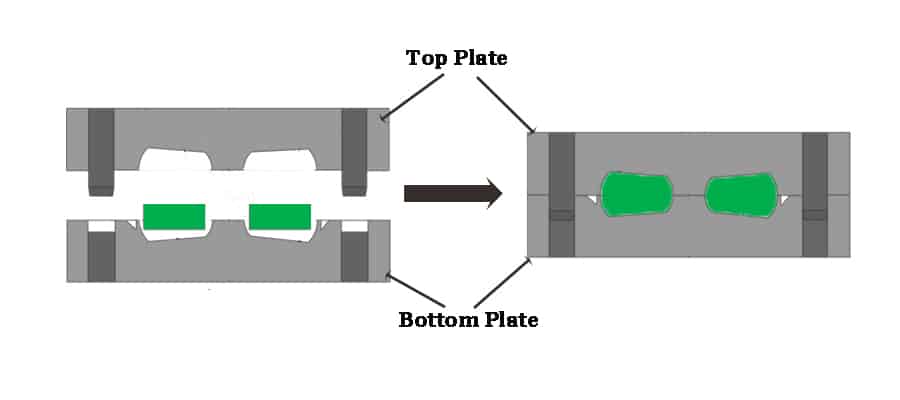
Silicone Compression Tooling
In reason of high elongation percentage of HCR and LSR, simple parts with mild undercuts are easily de-molded from two plates compression mold. Complex geometries normally require a pick-apart compression mold made of more than 3 different plates or actions.
Miwo typically apply aluminum and steel materials for silicone compression molds. Normally, aluminum mold can be machined and polished faster than steel mold, and it has a higher heat transfer rate in mold processing. This encourages us to produce an aluminum mold tool in as little as 5 business days with capable of 10,000 shots. Typical lead time of aluminum compression mold is 15 business days, however we also can provide 5 to 10 days in emergency sample projects.
In multi-cavity compression mold requirement, we recommend compression mold out of steel rather than aluminum. Steel compression mold tools will take 20 to 25 days to complete, in reason of its additional machining and polishing time.
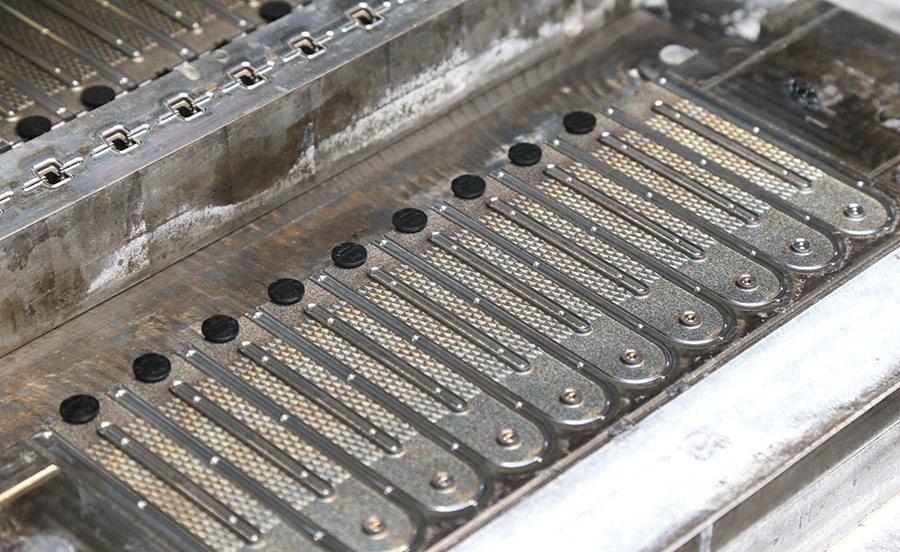
Silicone Compression Molding Benefit
- Short Develop Time: As silicone compression molds tooling is faster to machine with less cost, its development time is significantly shorter than Liquid Injection Molding (LIM). This could encourage silicone parts iterations to be completed in short time. Silicone compression molds can be modified for different revisions as well.
- No Gate Vestiges: There are no gate vestiges on silicone compression molding parts, as compression molds never require gates.
- Multiple Materials Application: Compression molds setup and breakdown time is significantly shorter than LIM, it also allows multiple materials’ application without any messy material changeovers.
- Easy De-molding and Inspection: As in silicone compress molding process, the mold plates are separated on nearby workbench, it is easier to de-molding and inspection. In addition, compression molds can be created with different part design in each cavity, which is more easily than LIM molds.
- High Efficiency of HCR: Compression molded silicone parts have the same quality, surface finishes, parting lines and flash tolerance as LSR injection molded parts. HCR (High Consistency Rubber) is easily molded in compression molds, while injection mold HCR requires complex and specialty delivery equipment with high cost and difficult production cycle.
- Cost-effective: Silicone compression molding can finish insert, fabric molding with simpler and faster development process, once comparing to silicone LIM. Silicon micro molded parts iares most suitable for compression molding, in reason of its shorter tooling and development time, lower overall cost.
Custom Silicone Compression Molding
Miwo has concentrated on silicone molding for 20 years, we are the most experienced manufacturer of HCR compression molding technologies. Our expertise encourage us to tailor the entire process for your specific demands, take your custom innovation into a new level.
We are the leading silicone parts manufacturer in China, we are able to serve all enterprise and companies in worldwide. Our advanced capability can encompass every aspect from design to production. We can assist you to select the perfect HCR grade, optimize design manufacturability (DFM), provide premium-quality tooling, high-volume production and packing solutions. Our high-quality HCR parts are widely applied in automotive, medical,
Contact us now for your new HCR compression molding project.